Written by: John Vanderhoof, LEED GA
Unfortunately, the perceived cost of going green is what deters most from building green and energy-efficient.
Let’s use light-bulbs as an example; if you were to see two light bulbs on the shelf that provided equal lighting, yet one cost $0.50 and the other $2.50 which would you pick?
Incandescent vs. CFL – We will use the life-cycle cost of 10,000 hours; the lifespan of one CFL.
Incandescent – lifetime of 1,300 hours, so we would need 8 bulbs to complete 10,000 hours of lighting. A single incandescent runs around $0.50, so our total cost for bulbs over 10,000 hours would be $4.00.
As it uses 60 watts, over a period of 10,000 hours, an incandescent bulb would use 600,000 watt hours, or 600 kilowatt-hours. At the current approximate price of $0.10 per kilowatt-hour, you would have to pay $60.00 to run an incandescent bulb over this period.
Total cost of a 60 watt incandescent bulb over a 10,000 hour lifespan is $64.00.
CFL – lifetime of 10,000 hours and costs around $2.50; only 1 bulb needed.
As it uses 13 watts, over a period of 10,000 hours, a CFL bulb would use 130,000 watt hours, or 130 kilowatt-hours. At the current approximate price of $0.10 per kilowatt-hour, you would have to pay $13.00 to run a CFL bulb over this period.
Total cost of a CFL bulb over a 10,000 hour lifespan is $15.50.
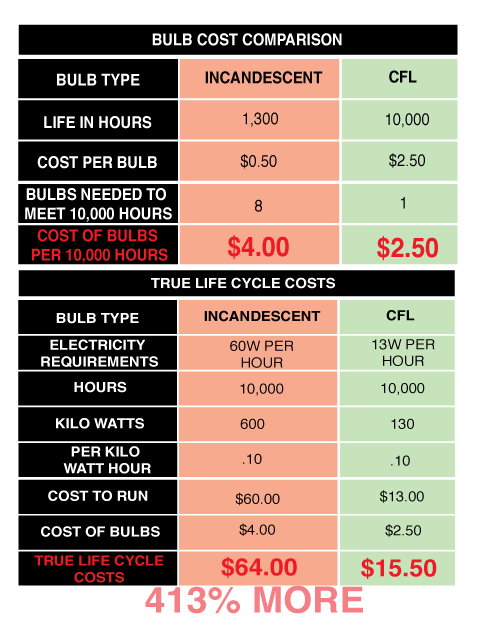
Bulb Analysis: Cost Comparison & True Life Cycle Cost
The incandescent ends up being 413% more while creating 8 times the waste and keep in mind we haven’t even figured in the environmental impacts of 8 times the manufacturing, packaging & transportation. Now that you understand the life-cycle cost, which would you pick?
The most criticized issue about constructing environmentally friendly buildings is the price…the cost of building. Photovoltaics, new appliances, and modern technologies (like the CFL) tend to cost more money. Most green buildings cost a premium of <2%, but yield 10 times as much over the entire life of the building. The stigma is between the knowledge of up-front cost vs. life-cycle cost. The savings in money come from more efficient use of utilities which result in decreased energy bills. It is projected that different sectors could save $130 Billion on energy bills. Also, higher worker or student productivity can be factored into savings and cost deductions.
Studies have shown over a 20 year life period, some green buildings have yielded $53 to $71 per square foot back on investment. Confirming the rent-ability of green and energy-efficient building investments, further studies of the commercial real estate market have found that LEED and Energy Star certified buildings achieve significantly higher rents, sale prices and occupancy rates as well as lower capitalization rates potentially reflecting lower investment risk.
So where do we start? Beginning with a resource efficient, well sealed and effectively insulated building envelope is crucial for any home to be considered “green” and sustainable. Through the successful incorporation of a high performance SIP envelope with other green products and practices, builders can cost effectively build to green, LEED, Energy Star and NAHB Green Building standards.
SIPs are made from thick EPS foam cores sandwiched between OSB (Oriented Strand Board) panel faces. The OSB is made from fast-growing trees, and produced in a way that yields a large percentage of every tree. The foam itself is made from partially recycled material, and the final result is a large solid panel that arrives to the job site pre-cut.
Job-ready SIPs allow installers to install the roof, wall and floor panels without the need to cut, frame and trim excessive amounts of lumber and other materials. The job-ready feature of Premier SIPs panels reduces the amount of job site material waste by 60% when compared to buildings constructed with regular dimensional lumber and framing materials. Less waste is obviously better for our environment. In some cases, we have had projects that did not have hardly any waste at all.
When compared to buildings framed with dimensional lumber, Premier’s large SIPs cover greater surfaces with far fewer gaps in the walls and roofs, to be filled and sealed, offering home and building owners better indoor air quality, reduced infiltration of outside pollutants, smaller HVAC systems needs and superior indoor temperature control. Premier homes and buildings stay cooler in the summer and warmer in the winter than buildings framed with dimensional lumber.
The R-Values are similar to those of other products. R-value is a static measurement of the resistance to heat flow. Premier SIPs have consistently outperformed other methods of construction in both whole wall R-value comparison and energy efficiency. Read our Technical Manager’s latest blog post- What in an R-value. The most dramatic results are the reports of the happy customers of PBS, but there is also a significant level of scientific data as well. One of the best measures of energy efficiency of an entire wall assembly has been developed by Oak Ridge National Laboratory (ORNL). This testing method considers energy losses for the structural members, corners, joints and around windows, as well as, R- value of the insulation. Contact us for a full copy of this report.
While most of us are willing to invest a 500% premium on a light bulb that yields a return on investment, why is it such a hurdle to get people to invest 2-3% more on a structure and using process that is environmentally responsible and resource-efficient throughout the building’s life-cycle that will provide an even bigger return on investment?
“We do not inherit the Earth from ancestors, we borrow it from our children” – Native American Proverb
Visit Premier SIPs website for more information, technical bulletins, specifications, details & more.
Visit the Structural Insulated Panel Association
References:
Architectural Engineering Study from Polytechnic State University- Material Sustainability, by Jessica Meadows & Natasha Morris
Energy Star
Easy Web Calculator